Stabilant 22A: All Scales
- Scott G
- Nov 24, 2021
- 4 min read
Updated: Nov 26, 2021
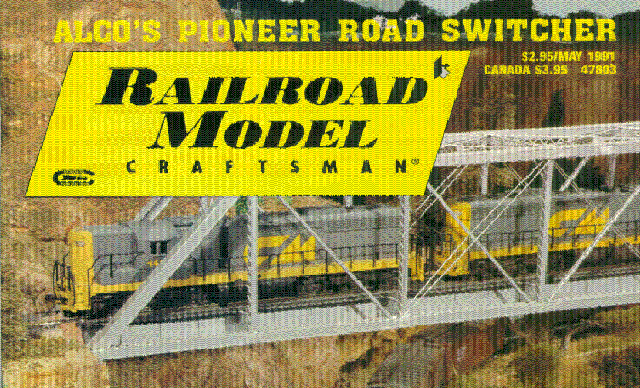
Manufactured by: D.W. Electrochemicals Ltd., 97 Newkirk Rd. N., Richmond Hill, ON L4C 3G4 Canada

Railroad hobbyists have employed a wide variety of liquid rail cleaners in the never-ending battle against dirt, corrosion, and tarnish, the prime enemies of good electrical conductivity and smooth-running equipment. These substances range from semi-caustic cleaners to sewing machine oil, and they work with varying degrees of success.
Stabilant 22A is a new product, described by its manufacturer as an "electronic contact enhancer," a material said to go one step further than a simple cleaner by chemically improving conductivity between two electrical contact surfaces, such as a wheel and railhead, or the pins on a plug-in connector.
Originally designed for use in the commercial electronics industry, Stabilant 22A coats the opposing surfaces of electrical connections with a liquid polymer carried by an alcohol base. According to the manufacturer, the polymer becomes electrically conductive between charged contact surfaces. If the surfaces have gaps, pits or small irregularities which lead to poor connections, the polymer is said to fill these gaps and, by way of its conductive properties, dramatically increase the contact area. The potential for improving wheel-to-rail contact, for example, is impressive.
The literature in the package says that long-term durability is the key to Stabilant's success and value. The brochure claims the product "Does not break down, evaporate, varnish, or react with any other chemical treatments previously used on the contacts."
In model railroad terms, Stabilant can be applied once to the rails, and it will continue working for a long time, up to a year or so, before it's needed again. The Stabilant chemical coating is said to deter the formation of rail-top tarnish, a feature which, in addition to its electrical contact enhancement, could be a real plus for model railroaders. The potential advantages for command-control or locomotive sound systems are obvious.
We started our Stabilant test by cleaning our nickel-silver rails with rubbing alcohol, a process which a company spokesman said was unnecessary unless the rails were heavily tarnished or physically clogged with dirt. As per the instructions, Stabilant was added to a cotton swab and applied to complete stretches of rail. It's possible to treat every few inches, skipping sections in between to allow the equipment wheels to spread the product, but it won't be as effective under these conditions.
Rails treated with Stabilant should be cleaned only by brushing or vacuuming, because liquid or abrasive solid cleaners will remove the chemical treatment.
At the club where the material was used, we haven't been able to verify any year-long performance results yet, but the trains continue to run smoothly on treated maintenance line sections more than four months after application. A hidden classification yard sees a lot of action, but engine stalls on turnouts and the like have been minimal on the Stabilant treated ladder section. Tractive effort on the grades does not seem to have been adversely affected.
A well used Rivarossi 0-8-0 switcher with a bad reputation for cantankerousness had Stabilant applied to its drivers, tender wheels, tender truck axle and pickup wipers. During a run session at the St. Joe Valley model railroad club in South Bend, Indiana, a group of on-lookers quit heckling and admitted being impressed as the 0-8-0 switcher eased through the yard "smoother than I've ever seen it run in years," according to one spectator.
We also conducted some starting-voltage tests with different types of locomotives. After recording the stock results, Stabilant was applied to the rails and the engines were run again.
The basic results are as follows:
EngineStarting VoltageVoltage TreatedOriental 2-4-4-2 (can motor)2.181.78Jonan 2-8-2T (can motor)1.371.17NWSL 2-6-2T (open-frame motor)4.954.6

All of these engines displayed smoother, less hesitant starting and running characteristics after the treatment was applied. It appeared that lower voltage was required to start and run the engines because current flow was improved, and less voltage was wasted punching through various resistance points as the current found its way from the power pack to the motor.
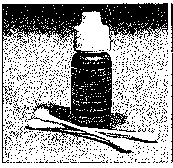
Railheads are just one area where Stabilant can be used. Power routing turnout points, relay, and switch machine contacts, overhead catenary, electrical plugs between modular layout sections, non-soldered rail joiners, turntable contact wipers the list is limited only by your imagination and ability to reach the contacts.
It can be reasonably argued that some of these improvements could be achieved with frequent cleaning and less-expensive materials. If the long-term effects of Stabilant 22A function as advertised, however, the savings in time and effort would be well worth the expense.
Personally, I'd rather enjoy the railroad rather than spend any more time cleaning rails than necessary, so Stabilant 22A may be one practical solution to this situation.
J. JOHNSTON
Courtesy of & Copyright © 1991 Carstens Publications Inc.,
Phil Harden Road, Fredon Township,
P.O. Box 700, Newton New Jersey 07860, USA
Stabilant 22A may be ordered from the manufacturer, D.W. Electrochemicals Ltd., 97 Newkirk Road North, Richmond Hill, Ontario L4C 3G4, Canada - Phone : (905) 508-7500